Optima™ Custom PDUs
Product SelectorConnect with Ethernet, Field Bus,
or Discrete Control Options ↑
Marway’s customization extends to remote power switching and monitoring. Our own RCM networking hardware and software (described below) provides Ethernet-based control of individual outlets and monitoring of inlet power over Ethernet using SNMP, RESTful API, and command line interface.
For simpler remote control, discrete signals can be used to toggle outlet power, to integrate safety of control interlocks, and provide indication of power state.
For field bus applications, we can incorporate industrial controllers to make control and monitor accessible over Modbus and other standards. Additionally, PLCs can be used to integrate custom measurements and control logic.
In all control scenarios, Marway’s Commander Remote EPO panels provide emergency off control for one or multiple PDUs.
- Remote control of individual outlets using Ethernet, Modbus, or discrete signals.
- Remote monitoring of power over Ethernet.
- PLC control to integrate custom interlocks and power data.
- Standardized EPO control for one or multiple PDUs.
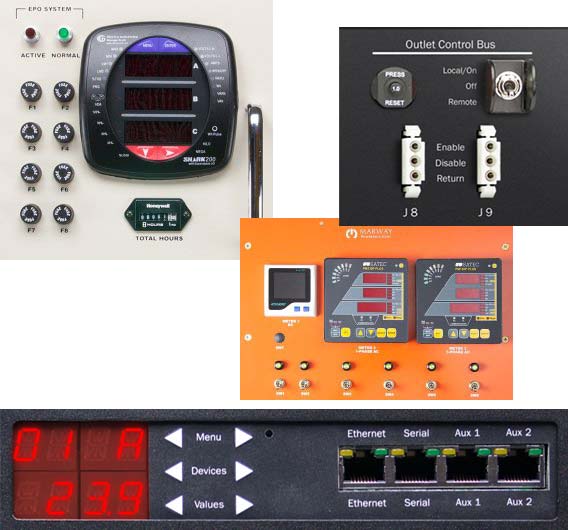
Click It or Script It ↑
Marway’s RCM Ethernet Software allows the remote control of power distribution outlets, and remote monitoring of power data. An operator can use a Web browser, a command line through Telnet or SSH, or SNMP manager or browser. Automated control can be scripted using a RESTful API (an efficient machine-to-machine protocol over HTTP/S), Telnet, SSH, or SNMP.
RCM software is available on Optima 8 smart PDUs and our Optima custom PDUs. Taking advantage of Ethernet networking, operators and equipment can be separated by walls or continents.
- Remote control of outlets (manual and scripted).
- Inlet current and voltage monitoring with setpoints.
- Display of watts, voltamps, voltamps-reactive, power factor, and frequency.
- Event alerts for startup, user login, outlet state change, EPO, power setpoint excursion, and configuration changes via SNMP, email, SMS.
- HTTP and HTTPS for web browser access.
- Telnet and SSH for command line access.
- SNMP monitoring, control, and alerts.
- RESTful API over HTTP/S to script outlet automation.
- Multiple users with independent login credentials.
- On-board activity log (SNTP time stamps).
- Ethernet 10/100-T, RS-232 serial console.
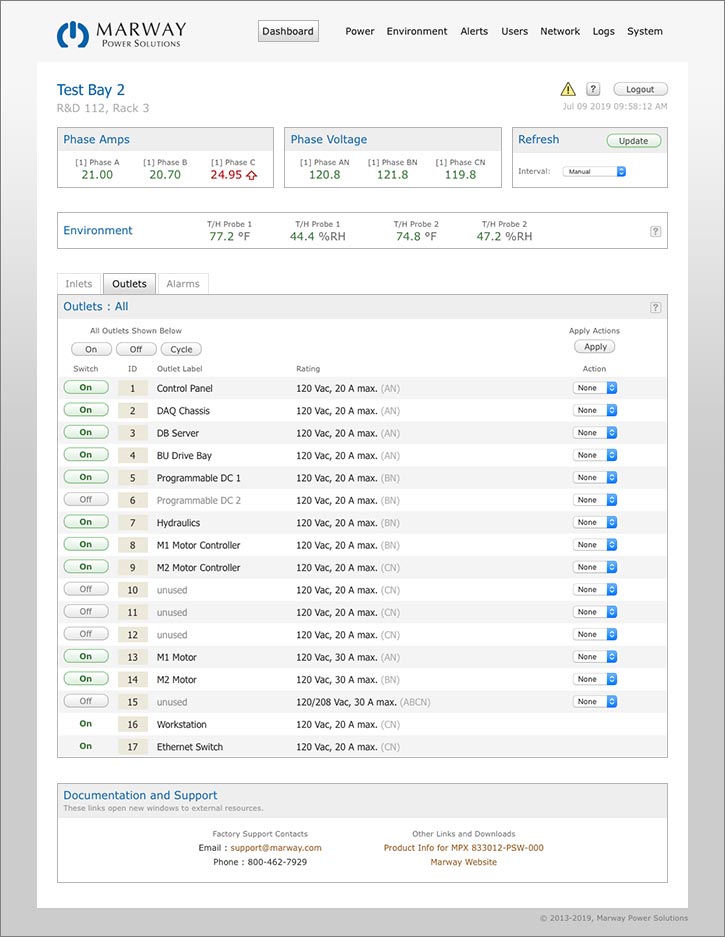
Outlet Control ↑
Each outlet may be labeled to reflect its purpose or what it is connected to. Each outlet includes on/off/cycle control with individually adjustable on delay, off delay, and cycle delay. Each outlet can be set so that during startup of the PDU, the outlet will be on or off, or whatever the last known state was prior to shutdown.
Outlets can be switched manually through web and command line interfaces, or remotely through SNMP. View RCM MIBs.
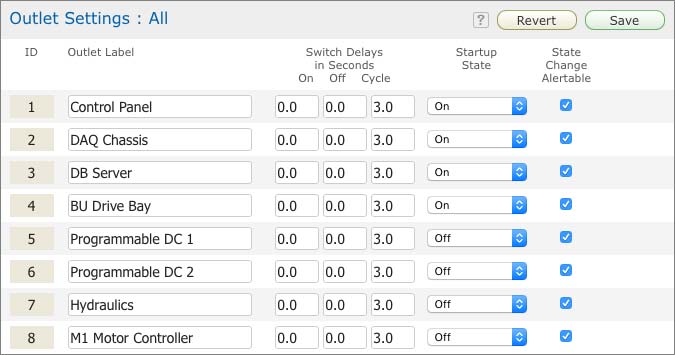
Scripting with REST or Telnet ↑
REST is a command and data exchange technique, commonly used by internet services, which is being recognized more and more in machine automation for its communication efficiency. URL-like commands are sent using the HTTP library of any programming environment, and responses are provided in simple text format. For example, with the RCM software, a GET /outlet/3/switch request will respond with either a simple “on” or “off” text value with no follow-up parsing needed.
Since RESTful APIs are designed to be machine-to-machine interfaces, using a RESTful API is easier to work with and more efficient than force-fitting the human-oriented Telnet/SSH interface for scripted automation with all of the accompanying string parsing (subject to breaking every software update).
While REST is the more modern and purpose-built option, the traditional technique of scripting the system’s Telnet/SSH interface is also possible.
Inlet Monitoring ↑
Inlet monitoring is available for single-phase and three-phase inlets up to 50 amps 240 Vac to provide comprehensive power data. Power monitoring measures volts, amps, watts, voltamps, voltamps-reactive, power factor, and frequency. Single-inlet systems can take advantage of a cost-effective current-only monitoring option. Acquiring inlet data can be automated using the SNMP, CLI, or REST interfaces.
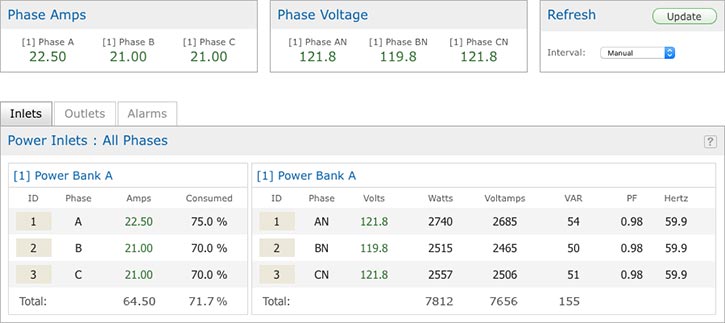
Alert Management ↑
The RCM firmware monitors several events including startup, user login, changes to configuration settings, setpoints for inlet current, setpoints for inlet voltage, EPO, and changes to outlet switch state. Each of these events can be routed to send alerts by email and SMS to one or more of the registered users (up to 20), and to an SNMP (v1,v2,v3) trap/notification receiver.
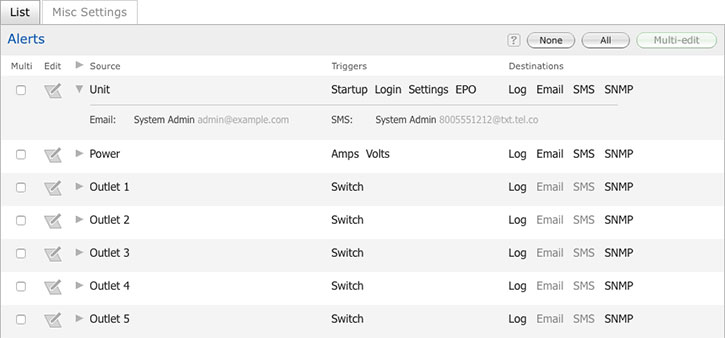
User Management ↑
Up to 20 unique users with independent login and permissions. Permissions segregate the ability to use and configure outlets, configure networking, and more. User profile fields aid in user identification and contact. Most recent login date and cumulative login count helps identify user activity.
On-board Logging ↑
An on-board log identifies recent activity including startup, logins, switch state changes, configuration changes, and more. Outlet switch logging can be disabled based on the protocol used so that known automated switching is not logged. The number of log entries is user definable up to 1000 events.
SNTP Time ↑
Support for SNTP allows the PDU to connect to network reference time server. This time is displayed on the Web interface, and is used by the on-board logging to time stamp recorded events.
Development Simulator ↑
The RCM development simulator (MES 802) enables developers of remote power control and monitoring software to develop and test code against a working RCM instance. This enables development of code for outlet control, power monitoring, alert notifications, provisioning, and doing pre-deployment testing of TLS certificates, and more. Having a simulator means this work can be done without taking a PDU out of commission, or without a full-sized PDU occupying the developer’s workspace.
- Runs on actual RCM firmware on actual RCM hardware.
- Only power data and switching behavior is simulated.
- Enables testing of all network APIs (SNMP, REST, telnet, ssh).
- Ethernet, serial, and temperature/humidity ports are all fully functional.
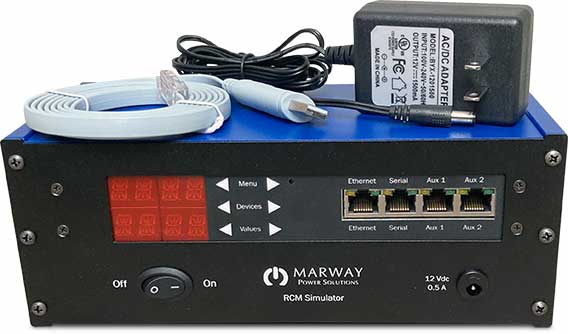